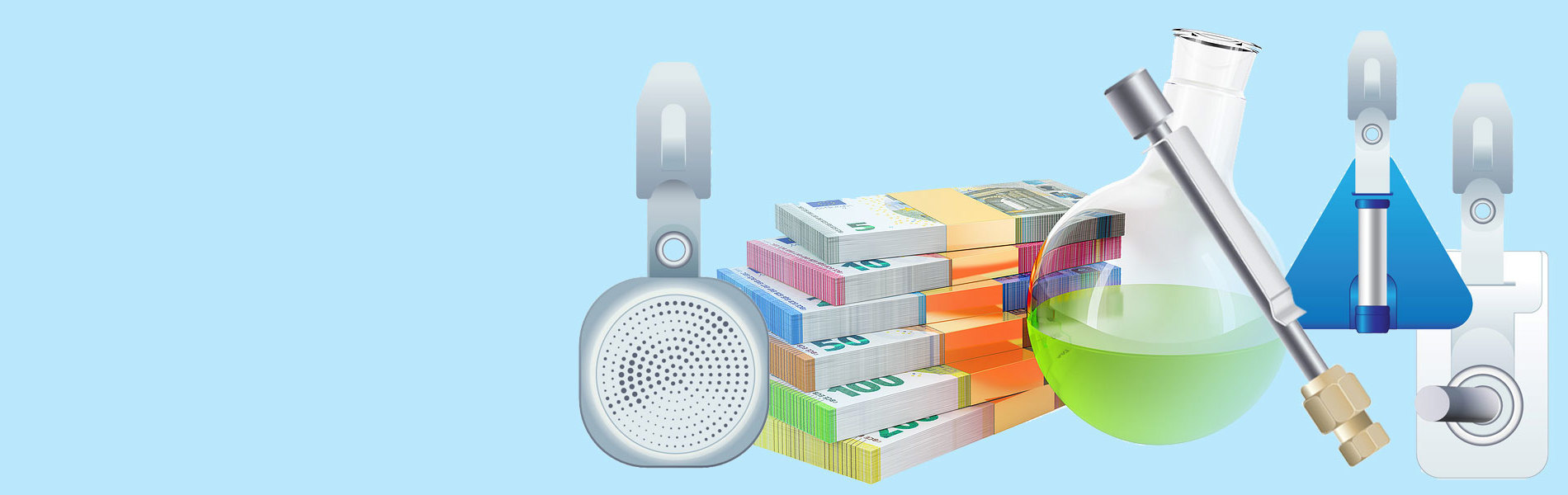
Passive sampling in the workplace: Why thermal desorption is replacing solvent extraction
17 May 2023
With the health and environmental impacts of organic solvents gaining increasing attention, analytical chemists are needing to justify every instance of harmful solvent use, and find alternatives where possible. With that in mind, Hannah Calder looks at why solvent extraction of sorbents (typically using carbon disulfide) remains so widely used for passive monitoring of workplace atmospheres, and shows that thermal desorption (TD) is not only better from a health & safety perspective, it’s better for lab budgets too.
Assessing the need for solvent
Solvents have been a mainstay of analytical chemistry since the discipline was founded. But with increasing attention now being given to the health and environmental impacts of once-commonplace solvents such as dichloromethane (see this latest US EPA announcement), using harmful solvents in the analytical lab is going to become ever more difficult to justify.
One of those uses is the extraction of sorbents used for passive sampling of workplace atmospheres, and related environmental health & safety (EHS) applications. A sorbent (typically charcoal) contained in a badge-type sampler is used to collect airborne volatiles, for example over the course of an 8-hour shift. The volatiles collected must then be released from the sorbent prior to GC analysis – and ever since passive sampling was used for this application in the 1970s, the preferred method has been solvent extraction (SE) with carbon disulfide, or CS2 for short.
Ever since they were invented, badge-type samplers used for workplace monitoring have been extracted by solvents such as carbon disulfide – despite the increasingly clear safety and performance drawbacks of solvent extraction.
What are the downsides of solvent extraction?
Unfortunately, CS2 has a rather long list of harmful effects, and with multiple manual operations involved in the extraction process, analysts must take precautions against exposure (the time-weighted average exposure limit is 5 ppm). Storing chemicals such as CS2 in the lab also takes up space, and places a burden on the analyst in the shape of paperwork, be that inventory management, risk assessments, or (should the worst happen) accident report forms.
SE is also less than ideal from a performance perspective. Solvent impurities, solvent-related baseline disturbances, and the dilution that is inherent in the extraction process all contribute to limit method sensitivity, typically to ppm-level atmospheric concentrations. At the same time, the desorption efficiency of SE can be badly affected for polar compounds in humid environments, placing another limit on method applicability.
Here, of course, is where you’ll expect me to point out that there’s a good alternative to SE, in the shape of thermal desorption (TD). This resolves all of the problems of SE, by eliminating solvent completely, improving sensitivity 1000-fold, and providing >99% desorption efficiency across a wide range of analytes even in humid environments. On Markes’ instruments at least, TD also now comes with the advantage of re-collection, which overcomes its historic ‘one-shot’ limitation.
Automated TD equipment such as Markes’ TD100-xr can eliminate all of the performance issues associated with solvent extraction.
Why bother changing from solvent extraction to thermal desorption?
So why does SE with CS2 continue to be popular for passive monitoring of workplace environments, and EHS applications in general? After all, passive sampling is commonplace for fenceline monitoring of industrial sites, but in this case SE has very largely been superseded by TD.
The difference probably lies in the unchanging requirements of EHS monitoring. Whereas other environmental applications have seen analytically challenging modifications to target lists and ever-decreasing reporting limits, for EHS applications, the target species have stayed largely the same, and the reporting limits have remained relatively high. So with SE remaining ‘fit for purpose’ from a performance perspective, and with its procedures encapsulated in several highly familiar standard methods, the drawbacks of handling toxic solvents such as CS2 can be tolerated.
Could that change though? With an increased focus on safety around harmful solvents, and pressure to eliminate them where possible, the amount of hassle involved in using CS2 is only ever going to increase – and if as an analyst you already find that aspect of your job a nuisance, that may be enough of a reason to switch on its own.
The financial case against solvent extraction
But there’s one further reason to move from SE to TD, and perhaps it’s more compelling than all the other reasons combined: money.
The financial burden of SE can be divided into the following aspects:
- Samplers: Unlike reusable sorbent-packed TD samplers, the charcoal samplers used for SE are single-use, resulting in large consumable costs.
- Laboratory fittings: Handling CS2 requires refrigerators and fume cupboards (or ventilated cabinets), which contribute to the lab’s energy demands – another cost that is eliminated with TD.
- Solvent disposal: Correctly disposing of waste CS2 is a cost that is inherently avoided with TD.
- Sample processing: Even if you have a solvent autosampler, the manual handling involved in SE is a cost that shouldn’t be ignored. In particular, it’s worth considering what you could do with the time you’d gain from switching to automated analysis on a TD instrument.
The ongoing cost of solvent-extraction methods may, for many labs, be the factor that tips the balance in favour of thermal desorption.
But is the initial capital expenditure on TD instrumentation offset by eliminating these substantial running costs? We did the maths, and worked out that the capital cost in switching from SE to TD would be paid back in under 2 years if your lab was running 50 samples a month, or just 6 months if you were running 250 samples a month… even without considering the additional revenue you might generate from having a TD system able to handle more types of analyses.
And in case you needed any further reasons to switch, TD analysis can now be carried out on reusable, fast uptake samplers, which provide the rapid adsorption of volatiles needed for short-term monitoring in EHS applications, while being just as lightweight and convenient as the conventional solvent-extracted type. As a result, you don’t even need to change your sampling method, providing one final reason to say goodbye to CS2.
Decision time for migrating from solvent extraction to thermal desorption?
So if you’ve been considering migrating from solvent extraction to thermal desorption for a while, but have never quite made a decision, maybe it’s time to have a fresh look at what you might stand to gain.
Analytical performance? Staff safety? Lab throughput? Or simply reduced running costs? Our new ‘Solvent extraction vs. thermal desorption’ infographic provides a helpful listing and explanation of the main factors, and shows how TD is increasingly cost-effective as you scale up sampling volumes.
Solvent extraction vs. thermal desorption - Key considerations when looking to switch
Techniques for sampling VOCs (volatile organic compounds) often use sorbents. Back at the laboratory there are two main methods for extracting and analysing samples, both coupled to GC(–MS): solvent extraction (SE) or thermal desorption (TD).
We compare the two techniques in terms of their cost and benefits to your data quality.
Already planning to switch to TD? If you need help talking through the options, then we’d be happy to discuss your sampling requirements. Just email sampletech@markes.com